The following is the transcript & the podcast audio for my interview with IvanTheTroll, originally released on June 7th, 2019. This is the special episode we did titled Gun Printing 101, wherein we covered all you need to know to get started in this new, exciting field of self-liberation!
[DOWNLOAD THIS TRANSCRIPT!]
Specifically, topics include:
- Terms/Types of Printed Guns
- Types of Printers
- Types of Polymer
- CAD/Software
- Where to buy gun parts/materials
- What not to do
- Listener Questions
- And much more…
The entire transcript for this discussion will be below, but it can also be found in physical format via A Vonu Guide to Firearms by Josiah Warren (click here or click the image below!).
And if you’d like to check out the full resources and show notes, please visit VonuPodcast.com/55.
Podcast: Play in new window | Download
Subscribe: Apple Podcasts | Android | Email | Google Podcasts | Stitcher | TuneIn | Spotify | RSS
GUN PRINTING 101 TRANSCRIPT
Shane Radliff: “What’s a 3D printed gun, Ivan? How would that be defined?”
[DOWNLOAD THIS TRANSCRIPT!]
IvanTheTroll: “There’s been a lot of discussion about this within gun culture itself, and even more so in our own little 3D-printed gun sphere. I haven’t really voiced this much but I sort of categorize it one of three ways. There’s primarily printed guns; those are going to be your Liberators, Songbirds, or Washbears, where there’s maybe one or two metal parts, like a firing pin or a barrel liner, but everything else is going to be polymer printed. Those guns of course have their drawbacks. I think to date they’re almost all single shot. The limitations of plastic mean you’re going to be limited to a small number of shots. The Songbird can do 20 or more, I’ve heard as high as 50 on some Songbird barrels and 22 long rifle.
The Liberator can do maybe 10 at the most. So, there’s a couple primarily printed guns, but they’re probably the least common type of design. And I mean, probably also the least viable as far as an extremely effective firearm because most if not all are single shot. The second tier, then, as I sort of touched on, is a composite firearm. What I mean by that is it’s a matrimony of plastic and metal parts. Examples of this would be Darwin’s AP nine, our upcoming FGC nine. There’s a couple other designs out there, but, in general, the gist of it is you use hardware store parts in conjunction with printed parts, your end product is a firearm that would work as well as an off-the-shelf or gun store firearm.
So, there’s no like strict definition in my mind for a composite firearm; it’s just a gun where, whenever you look at it, you see that most of the parts are printed. The AP nine is a good example, where the uppers, lowers, and buffer tubes are printed. You could see it’s got a steel barrel sticking out the front and that it’s got an AR15 off-the-shelf fire control group in there. But otherwise, it strikes you more as that it’s a printed gun, not simply because lots of the big parts are printed. And so the final echelon in this three-tier thing is a printed component. In the United States, firearms are regulated in a way that only one part is deemed the firearm.
In an AR 15, it’s the lower receiver. The ATF, the rule they try to stick to is it’s whichever component accepts the fire control group parts. That’s the trigger and the hammer, or your Stryker setup. But there’s exceptions to that. Like, on the FN FAL or any FAL-pattern rifle. It’s the upper on those that is regulated, and not the lower. So, even though the lower on those has the trigger and the hammer and all the trigger components, they regulate the upper instead. The HKG3 and MP5, all of those stamped, roller-delayed guns that HK made, are all the same way, where the trigger components are not regulated. It’s the stamped upper that is. So, the ATF doesn’t always stick to that strict definition.
But in general, I don’t think there’s any examples of there being more than one regulated component on a single gun. So, the ATF says the lower receiver is regulated on an AR 15, that it’s the gun and no other part is. By legal definition, then, if you print that lower receiver, you can say it’s a printed gun, because that’s the only part there that constitutes a firearm in the eyes of United States law. So it is a little bit of a misunderstanding and, like, a misnomer, because somebody will say, “Look at my printed AR 15,” and all they’ve done is printed the lower. But, by legal definition, it is a printed AR 15 and I don’t really take any objection to someone saying their printed AR 15 lower is a printed AR 15.
And this goes on, but I’ll try and keep my tangents shorter on this show.
But this goes down a tangent, because our group was discussing this at length. People call glocks “polymer pistols” or “polymer-framed pistols,” but, in general, they are referred to as plastic handguns in gun nomenclature. We all realize the glock has a steel upper, barrel, and fire control components. It’s not an entirely plastic gun as you would think, if you hear “polymer pistol.” In the early, early days of the M16, like my grandpa still refers to AR’s as plastic guns, simply because they had plastic furniture everywhere; that had shock value back in the 1960s, whenever the M16 was new. People refer to it as a plastic gun and thought it would be weak and break easily, because it’s covered in plastic; they were just coming out of the era of Bakerlite, when plastic was incredibly fragile stuff.
But, for that reason, the AR 15 was referred to as a plastic gun and then later in history, like throughout the 80’s and 90’s, as well as some in the 60’s, 70’s, you see the AR 15 referred to as an aluminum gun, while we understand that the bolt, the bolt carrier, the barrel, and many other components are still made of steel. People still called it an aluminum gun, simply because there were components of the gun that were aluminum and that was novel then. Not every gun, in fact, very few guns were made of aluminum parts. An aluminum receiver, that was like a get out of town sort of thing back in the 60’s and 70’s. So, it was referred to as an aluminum gun.
Now, in the 21st Century, whenever we say we have a 3D printed AR 15 for the same reason, I don’t see a problem with calling it a 3D printed AR 15, because you’ve taken a part that is traditionally made, not in a 3D printed way, and you’ve printed it. No matter what, though, the trolls will show up and try and say, “Well, you didn’t print the entire thing,” but so long as you’re like, “No, I didn’t, but by legal definition, it’s a printed lower, and this is a novel thing that I have here, right?” I’m not trying to say the entire guns printed. What I’m saying is I’ve printed a critical component of the gun, which is legally the entire gun.
~~~
~~~
Shane: Very interesting. I suppose the next thing we should get to is types of printers. Now, we talked about this a little bit in our first discussion. They’re kind of different stages. Obviously, if you’re willing to pay a high enough amount of money for something, someone will probably be willing to supply it. So, I guess let’s go on and get to the types of printers, I’ll turn it over to you. Walk us through the various types of printers.
Ivan: Last time we had talked about the metal printers, and I’ll touch on them again briefly this time, although I won’t go into how they work, because if you’re really that interested, go to the other show. We’re essentially just going to cover that there’s two different ways in which metal printing is done. First, using a direct laser-centering process or it’s done using a centering process, like a post-process centering. Both of them are really cost prohibitive at this point, although that may change in the future. But again, go to the other podcast for more information on that.
When it comes to consumer-friendly stuff, there’s really two main kinds of printers that you run into, with a third one that’s going to become affordable within under five years. The most common one, the one that everyone is used to, is the FDM, “fused deposition of material printer.” It’s also sometimes called “fuse deposition modeling printer”, and also sometimes a “fused filament fabrication printer.”
Again, like we had talked about in the other podcast, each kind of printer has like four different names attached to it, and they all mean the same exact thing. But FDM, the way that works, in a nutshell, is picture a hot glue gun. It’s got a hot nozzle and you squeeze the trigger; it squirts that glue out of the hot nozzle, because the nozzle will melt it. Now picture, if you took that hot glue gun, and you set up a robot to pull the trigger at very precise levels, increments, and rates. Then, you set up a robot arm to move that hot glue gun in very specific patterns. And now imagine that the robot now understands it can print one layer by moving this hot glue gun around and leaving a very specific path of hot glue.
Then, it can move up a layer, and then up another layer. That’s exactly what a FDM printer is. It’s a glorified, computer-controlled hot glue gun and it works essentially the same way, except it’s got a computer controlling it. So, there’s like those five minute hacks or whatever that were popular, I think they might still be popular on YouTube. I haven’t been on YouTube in a long time, but there are people who are using hot glue guns as like manual 3D-printers. They would like build a shape out of a hot glue gun. So, if you’re familiar with what that is, this is just a computer doing that for years. FDM printers are the most common kinds of printer by far and away. And they’re the cheapest kind of printer as well.
The printed gun community, including the new folks that were getting into it, we’re standardizing them on the Creality Ender 3, which is a Chinese-made printer. And don’t let the “Chinese-made” scare you away, because they’re made quite well. The experience that these new people have had with them is quite positive. I think we had a guy that, within one week of getting his printer, had printed a usable Glock 17 frame, which is just awesome. But in general, that’s the FDM printer. If you’re interested in getting into it, it’s a Creality Ender 3. You could probably just search for it on Amazon. They’re $200, but sometimes go on sale for $180 with free shipping on Amazon within the U.S.
So, a step above that series of FDM printers, would probably be the Prusa series. FOSCAD still recommends the Prusas over the Enders and I mean, depending on what your budget is, I would agree. I would go with a Prusa over Ender. Prusas are sitting at, I think, $800. Now, when I bought mine, they were $650, but they’ve gone up in price; that said, they’ve also gone up in the number of features they have.
So, I’ll stop here and we’ll get to the other kinds of printers in one second, but what I’d like to talk about now is the features and advantages between the Creality and the Prusa; because I constantly get asked this question, I think it’s very relevant. Whenever you get the Ender, it’s the bare minimum a printer should be, at least in my opinion: it’s got a heated bed, it’s got a good structural setup, it’s got a metal frame. That’s basically what I’m trying to get at. So, there’s like the bare minimum you would want in a printer with no extra frills.
There are printers priced between the Ender 3 and the Prusa that offer you one feature or the other. The Prusa essentially offers you all the nice features in a cheap FDM printer that you would like; the Ender offers you essentially none of them, but the Ender is upgradeable to some extent. So, the main differences between them is the Prusa offers you a quick detachable bed; the new Mark 3 does, I believe. It comes standard now with a detachable bed, which is super cool, because it makes it easier to get your prints off the bed. And the new Prusas come with automatic bed leveling.
One of the hardest things with the Ender is you have to make the bed perfectly square to the nozzle, and if you don’t, your prints end up looking wonky. The Prusa does that for you, which is quite nice. Once you’ve learned how to level a bed, it’s not a problem on the Enders, it becomes something that you don’t even really have to think about. But if you want to cut out that part of the learning, the Prusa does that. The Prusa also comes with the hot end that isn’t a plastic on heater block hot end.
So, without getting too deep into it, 3D printers use a Teflon tube to guide the filament down to the hot glue gun. If that Teflon tube touches the heater block, which is the hot part. As some of you may know, right around 250° Celsius, Teflon starts to release the gas that’ll make you sick; it makes you queasy and sleepy and all sorts of not good stuff. And it’ll kill pet birds if you’ve got pet birds. So, the Creality’s are like software limited. They won’t go above like 245°; they might be able to go to 250°, but I think 245° Celsius is the hottest they will let themselves go. So, the Prusa uses what’s known as a heat break, meaning the Teflon tube does not touch the heater block directly. Because of this, the Prusas can go above 300° Celsius and you’d be fine, but their software limit is 300°. Getting above that temperature requires all sorts of different changes.
In general, 300° is the hottest you’re going to get from an affordable printer. I think, in order to get above 300°, you’re now looking at like a $2000-$3,000 printer. So, between the two, probably the weakest thing then on the Ender is that hot end, because you’re limited at 240°-245° Celsius, which means there’s some high strength nylons the Prusa can do, that the Ender can’t. Now, you can upgrade the Ender with a micro Swiss hot end. There’s tutorials all over YouTube about how exactly you install that upgraded hot end. So, whenever the Ender is running that hot end, it does have the same temperature range it can print as the Prusa. I guess one other notable difference is that the Prusa comes with a nice glass bed, whereas the Ender comes with like a crackle-finish bed.
A lot of people swear by the Ender 3 stock bed not working. I’ve never printed on a stock bed Ender 3, so I wouldn’t know at all. I’ve printed on a buddies and he’s got a glass bed for it. So another upgrade that the Ender could use, is a glass bed, and those aren’t terribly expensive at all. But, aside from those two differences, I guess the Prusa has more build volume, something you always need to be aware of, as a printer has a limited space that you can print in, known as a spread bill volume. The Prusa has a slightly larger build volume. That said, you can print AR lowers, Glock frames, and Glock magazines on both. So, it’s not like the Ender is running out of room for certain projects, but at least so people are aware, the Prusa does offer a little bit more print area.
That about covers FDM printers.
The other kind of printer that’s out there in the consumer market is known as SLA. So, I can’t explain SLA as eloquently as it’s a hot glue gun with a computer. What SLA is, is picture you’ve got like a vat, and that vat is full of a liquid, and that whenever you shine a light on it in a particular spot, that liquid gets hard. That’s essentially how an SLA printer works, is it’s got this vat of UV hardenable, UV-curable resin in it, and it’s got a UV laser at the top of the printer. So, it fires that UV laser down in that specific pattern that it wants to harden, and then some versions increase the level of the fluid, some of them lower down the bed that it was already printing on. But either way, the effect is the same.
You zap your resin and you harden it, and then you increase it so the layer of the liquid, the resin, is now one layer above where it is that you just hardened, and then you harden the next layer. So, you just use the laser to harden layer-after-layer, one-on-top of the other. SLA printers are generally more expensive than FDM printers. SLA printers almost always don’t have as big a build volume, and SLA printers are generally not as strong either. FDM printers, you can print some really, really strong nylons on. SLA printers are kind of lacking as far as the strength goes. The big advantage to SLA is if you’re interested in using your 3D-printed parts for 3D printed-assisted casting, SLA printers can print with very nice surface resolution.
Whenever you run your finger along the side of the part, it won’t feel like its 3D-printed; it’ll feel like it’s just a normal part, whereas on FDM printers, essentially you can always feel the fact that it was printed because there’s layer lines that you can run your finger along. Then you can see those layer lines in pictures, of course. So, I think as far as affordable SLA printers go, I know Prusa has a new one that, I think, is $1300, but I’m pretty sure you can’t fit an AR lower in it. It doesn’t even have my attention. You know, maybe one day, they’ll make a bigger one and I’ll be forced to buy it, just to print an AR lower on it to say I’ve done it.
Then, the last two things to touch on here on the subject of printers.
The first one being that printer that I mentioned, the new technology that’s coming. Form Labs has a printer that uses selective laser centering of nylon. So, the same way I talked about last podcast, there’s the printers that can zap a metal powder with a laser and then fuse it together. That same kind of printer can be used to print nylon parts that way. And Form Labs has a machine and I think it’s called the SLS1. And I think they asked like $3,000-$5,000 for it, which is pretty cost prohibitive. And it might be more than that because I might be confusing it with another printer. But the Form Labs SLS1 does this process of laying down a sheet of powdered nylon and then a laser in the top of the machine will fuse the nylon with the correct layer, while the rest of the of the nylon remains unfused.
So once you’re done, you brush off all this powdered nylon that worked as support material and now you’ve got your centered part this way. And the surface finish on that is generally incredible, and you get excellent layer adhesion, because you weren’t melting it out of some kind of hot glue gun, you were really fusing it with a laser, so it ends up producing a little bit stronger parts that way. I think, at this point, that those Form Lab printers only work with nylon, but nylon is an incredibly powerful material; there’s nylons that are hard and inflexible, or soft and flexible, and there’s nylons in between. Nylon is a very wide range of things, so that’s something to keep an eye on. If those SLS nylon printers get a little bit cheaper here in a couple of years, I would start recommending those over FDM just because there’s less issues that you’ll run into with that, the SLS printers though, the laser-centering ones.
~~~
~~~
Shane: Very good, definitely interesting. $200. I didn’t realize it was that cheap. I might have to hop on this, too, just start messing around with it. But anyway, I guess the next point of discussion here would be the types of polymers. I think there’s PLA, ABS, nylon, PEGI, and there might even be some other ones. Let’s talk a bit about the various types of polymers.
Ivan: Sure. As you mentioned there, those four are probably the big ones. If you get an FDM printer, I would say those four are probably going to be your mainstays. I’ll just run down the list there. I’ll give some relevant properties, tips and tricks, and printer settings that I like to use for each of them. PLA Plus also falls under this category. PLA Plus is controversially stronger than normal PLA, some people think it is, some people think it isn’t. Some tests show it is, some tests show it isn’t. I like PLA Plus, just because it comes in nice colors; it comes out kind of shiny, so it has a nice surface finish on it when it’s done, as well as the fact that I think PLA Plus prints easier than PLA.
But I should also explain, PLA prints easier than any filament out there. PLA was specifically formulated to be able to print really, really nice. So, it prints at relatively mild temperatures. I like to print it at 235° on the hot end, and then 60° on the bed. It’s normally recommended that you print at 205° on the hot end. I find that if you print it hotter, the part will end up coming off the bed much stronger and printing PLA plus or normal PLA at 235° doesn’t cause any…well, normally, the hotter you print, the worse the surface finishes; like, the more ugly the part is. I haven’t had any problems printing at 235°, so I recommend 235° on the hot end and 60° on the bed for printing PLA.
As far as tips and tricks go, using glue stick can help some, like if the corners of your prints just want to warp up. Something you need to consider with FDM printing is you’re printing this plastic at 230° Celsius and it very quickly cools to room temperature. As it’s cooling, as I’m sure everyone remembers from like high school or even before that in science class, things that are hot expand and things that are cold contract. So, once this plastic starts to cool, it tries to contract, which means there’s constantly this contraction force coming towards the middle of the part. And so because of that, I’m sure there’s people who have been printing, say, the AR lowers and you have the corners of the lower start to warp off the print bed.
And if you have them warp enough, it ruins your print because now the entire part will try and warp up. And if it gets really bad, the entire part will warp to the point where the whole thing pops off the bed, which is really unfortunate. So, some ways to combat that with PLA: Normally PLA doesn’t warp much, but if you print at high end fill and a part like an AR lower where it’s really long, and it doesn’t have a lot of surface area, it will try and warp with PLA. But you can use glue sticks, like a cheap Elmer’s glue stick, slather on a thick layer on the print bed where it is that you set your part up to print and go ahead and print on top of that glue stick. You can remove the glue stick later using acetone or using saltwater. It won’t damage your bed at all to use a glue stick, of course.
And a glue stick is like nontoxic and safe, because kids eat it or whatever. Using PLA on glue stick is a good option for keeping those prints stuck down a little bit better. And that about covers my tips and tricks for PLA. Really there aren’t a lot of tips and tricks, it’s very easy to print with, very nice stuff.
Shane: And like how much does PLA run? Price-wise?
Ivan: Like $20/kilogram, which is cheap. So, you can can be printing off AR lowers—well, I don’t recommend you print AR lowers in PLA, as like a last resort you can. You can, but I should’ve mentioned properties of each of them. PLA is very stiff but it’s very brittle, and this is because whenever PLA gets hot and then cools, it crystallizes.
If you think about glass and of course it’s not as exaggerated as for glass, because glass is incredibly hard, but incredibly brittle. PLA is of course less hard and less brittle than glass. But the same way that glass is like it is, where it doesn’t want to break, you could push really hard on a glass window, but before it budges at all, it just shatters. PLA is a lot like that. PLA has a little bit of flexibility to it, but before it flexes too far, it just wants to break, it’ll shatter. And that’s because it has an internal crystalline structure, sort of like glass does, sort of like diamonds do. And so because of that, it has almost no flexibility to it, it has almost no yield. It just instantly goes to breaking, which means that it’s as far as its fatigue properties go, cycle after cycle after cycle, it’s really bad.
And if you look at an AR lower, right at the buffer tower, all those forces that it’s going to see, they’re like cyclic. What that is, is fatigue forces going crazy there. So, as your gun recoils and it recoils and it recoils, it puts a fatigue force in your buffer tower because it’s, you know, cycle after cycle. With PLA, you’re going to have to hope that the recoil forces aren’t enough to deflect your buffer tower at all. And, generally speaking, they are, if you use a 22 long rifle upper, of course, it’s not gonna happen; but in .223 or anything bigger, including 9mm because 9mm is direct blowback in AR uppers, so it has recoil forces on par with .223. Because of that, for essentially anything besides 22 long rifle in an upper, a PLA is not a great idea for your lower because those fatigue forces will eventually get it to shatter.
The solution there is to use a material that’s got a little bit more flex to it, as well as a little bit more strength overall to it. And that material is ABS. ABS is the same thing that Lego bricks are made out of, which is super cool. And ABS has a lot of neat properties to it that oftentimes don’t get taken advantage of. I’m going to first address the problems with ABS because there are problems with ABS.
The first problem is it’s supposed to cause cancer. The fumes from hot ABS are supposed to cause cancer and that’s not like a “Known to the state of California to cause cancer.” It’s like a, “Research papers have come up saying it might actually definitely cause cancer.” I don’t know that I’m super concerned about it, but it is something that you guys should probably take note of.
I print in a small room that smells like ABS 24/7, so I’ve probably got my lethal dose by now, anyway, if it is as bad as they say. But it could also just be like, for awhile, they were saying hot dogs are like guaranteed to give you cancer. But then they backtrack on that thing, maybe not. So, I don’t know. It might be one of those things that it might end up just being a “Known to the state of California to cause cancer.” But it might actually be a risk. So, if you do print in PLA, you should exercise good judgment and do it in a ventilated area and not in a small room…or you can just do whatever you want. Don’t let me tell you what to do, but it might cause cancer. So, be aware of that. Also the fumes just smell bad. It’s not pleasant.
The other problem with ABS is, so I had mentioned PLA warps a little bit, ABS warps a lot. So, as it cools, it shrinks significantly. And because of that, it will really, really want to warp off a print bed. There’s a couple of solutions to this; the industry standard solution, and I shouldn’t say industry, the hobby standard solution, is to put an enclosure over your printer. What an enclosure is, it can be something as simple as a PVC frame that you throw trash bags on top of, but you’re trying to trap a little bit of heat around the printer. The printer is printing in a warm environment. And so whenever you do that, the ABS won’t be able to shrink as quickly, meaning it’ll shrink more gradually. Therefore, it won’t work off the print bed.
So, ABS is still of course shrinking because that’s what ABS does, but it won’t grab your part and warp it off the print bed while it’s shrinking because it’ll shrink slower. That’s the idea behind an enclosure. Now, a solution that I have found and I exercise because I don’t want to have to build an enclosure. The solution I use is a technique that’s known as ABS glue. Some places sell ABS glue. I wouldn’t buy ABS glue from anyone because it’s very easy to make on your own. The interesting property of ABS is that it dissolves in acetone. So that may mean, “Okay, cool, I can stick my Lego bricks in acetone and they turn into a liquid.” But that means a couple things for 3D printing.
The first being you can take some of your scrap ABS, dissolve it in acetone until it’s completely liquid. Then, pour that mixture on your print bed in sort of like a thick layer. Use like a straight edge or I use like a Popsicle stick, and if you tap the Popsicle stick, you know, going left to right, and then right to left across the print bed, you can get a nice level layer of ABS, and whenever that acetone evaporates off, you’ll be left with a layer of ABS across your print bed. If you print your ABS part on top of that layer of ABS that you applied using the acetone, your print will have a very hard time warping off. It will not want to warp off. The problem with this becomes that your part will stick to the print bed so well you’ll have to like get creative and use chisels and take a whole lot of time in order to get your part off the print bed. It will really, really, really stick down if you use a thick layer of ABS, but the upside there is it didn’t warp off.
The other use, then, for ABS dissolving in acetone is if you have two parts made of ABS and you paint acetone on one part, and then on the other part, and you stick the two acetone surfaces together, you can weld the ABS parts together that way. That becomes incredibly abusable to the point where you can print two parts separate, paint them with ABS, stick them together, and then stick them in a clamp and let the acetone dry; when you come back, it will be fused together like it’s one part. It also means that you can polish ABS that way. So, if you can stick, say, a five gallon bucket over the top of an open bottle of acetone and your printed part, and then you come back and check in 30 minutes, your part will be shining all over the surface, like the layer lines will start to disappear because acetone will evaporate into the atmosphere underneath your bucket, and it’ll settle on your printed part, smoothing the layers on your printed part. That increases the strength of the part and makes it shiny and smooth on the outside, as well as you can then use it to weld parts together. So, ABS is very, very cool for those reasons.
As far as print settings on ABS go, I usually print it at 265°, although you can print it as low as 250° and it works fine. I haven’t really noticed a difference in strength printing 250° versus 265°, and for bed temperature, do 100° Celsius. I think that about covers ABS.
Shane: What about the price for ABS? PLA was, I think, $20/kilogram?
Ivan: There’s a couple grades of ABS. You can use Chinese ABS. For PLA, I recommend like eSun or Hatchbox PLA, you can use the cheap Chinese brands.
For ABS, I recommend the more expensive brands of ABS, just because I think it works a little bit less. That said, you can use the Chinese ABS, it’s tested about $20-25/kilogram. The more expensive American stuff, the company that I use is called IC3D. There’s rumors that go around that say that their ABS is just like re-spooled Chinese stuff that they’re selling for more expensive. I don’t buy it because it warps less and I think it ends up stronger. But, you know, maybe that’s true and I’ve just been fooled. But my tests and analysis suggest that I have not been fooled. And the IC3D is a little bit better. It runs like $45/kilogram. So it’s essentially double the price. But I would say it’s worth it if you’re new to printing ABS, learn on the Chinese stuff, because if you can print the Chinese stuff, you can print any ABS.
Shane: Alright. I guess the next one would be a nylon?
Ivan: With nylon, there’s a lot of confusion. In the early days of printing nylon and FDM, it was very difficult because the chemists that were making these batches of nylon for 3D printing were just taking normal blends of nylon and then making it into a filament form. The problem with that is nylon doesn’t really like to stick to stuff, and so people were having a really hard time getting nylon to stick to a print bed; it would want to warp off and nylon shrinks probably more than ABS does as far as it’s shrinkage rate as it cooling. Some people had a lot of trouble printing in nylon for a little bit, meaning there’s a lot of essentially FUD out about how nylon is hard to print.
With modern nylons, for example, DuPont’s ZyTel High Strength nylon, I don’t think it’s possible to have problems printing it. It prints so nice and so easy and so smooth. There’s a couple other taulman-grade nylons out there that I have had reported to me that also print really, really nice. Nylons are in general stronger than ABS, more flexible than ABS, and have the added benefit of modern ones warp a lot less than ABS. As far as tips and techniques go, a glue stick works with nylon, as far as getting it to stick down to the bed some, because sharp corners, like on AR lowers, will still warp up with nylon, but if you use a little bit of a glue stick, that’ll be avoided.
As far as getting really, really strong parts, nylon is generally the way to go. DuPont now sells fiberglass impregnated nylon. There’s Zytel impregnated with a fiberglass. It’s the nicest printing filament I’ve ever used to the point where I’ve printed AR lowers with literally zero work. Incredibly strong filament, it ends up being as strong as selective laser-centered nylon, which is kind of hard to believe, but it does do incredibly well. And I’d have a couple, I think several, lowers now printed in it and it’s very, very strong stuff. It makes excellent lowers and it makes excellent Glock frames as well. I give my recommendation to both of those DuPont plastics. The problem with them is they’re expensive; I think it’s like $100 for normal Zytel/ kilogram and then $110 for the fiberglass stuff. So, it’s awfully expensive, as well as stock Ender 3’s cannot print the fiberglass stuff; and to print the fiberglass stuff at all, you need a hardened steel nozzle, because fiberglass is abrasive, of course. Stock Enders can’t get hot enough to print the fiberglass stock.
Really, you want to print both the normal Zytel and the fiberglass Zytel at like 280° Celsius, which of course the Ender can’t do. But you can print the stock Zytel, non-fiberglass Zytel, at 240°. It’s just that the layers won’t be very well fused at 240°. So, in general, if you want to print Zytel, you need the upgraded hot end for the Ender, or the Prusa that is entirely capable of it. I print all my Zytel on a Prusa.
There are other grades of nylon. I consider Zytel “high strength nylon”, which is how DuPont describes it. There’s other, say, mid-tier grades of nylon, like the ones known in the industry as Nylon 6 or Nylon 66.
There’s all sorts of taulman grades that start with a six, and there’s a couple nylons that start with a 9 like Nylon 910. The problem with nylon becomes, like I was talking about earlier, that nylon means a lot of different things and there isn’t just one nylon. But, in general, nylons are great for printing AR lowers, they’re great for printing Glock frames. It’s fairly easy stuff to print with once you figure it out. The glue stick works well with it, but print settings are going to vary based on the grade of nylon you have. In general, you want to print it hot in general, your printed bed’s going to want to be hot, but again, nylon is a great big mixed bag. There’s lots of it, and most of what’s nowadays is like optimized for 3D printing. So, DuPont’s Zytel filament is optimized specifically for 3D printing. That’s probably the reason why it doesn’t warp much at all, because they specifically made it not too warp.
Shane: I have a question. How many AR lowers could you print with $100 worth, 1kg, of that nylon stuff?
Ivan: I want to say you’re guaranteed five whole ones, but it always depends on how you set up your supports and then if you fail any prints as well. I think I’ve gotten five AR lowers and a Glock frame out of the current roll of fiberglass I’m printing on, the fiberglass Zytel. So, I want to say that you can do maybe six AR lowers off it. But again, it depends, and I should’ve talked about this earlier, but there’s a thing known as infill in 3D printing. And what that is is, since you have a 3D printer, you have control over geometry, so you don’t have to print your part solid if you don’t want it. You can print it so it’s 10% hollow on the inside all the way up to 90% hollow on the inside.
The first AR lower I got to print that worked well, I printed at 30% infill, which means it was 70% air on the inside and ABS, and I’ve got 2000 rounds through that lower. I ended up decommissioning the lower just because of the buffer tower was starting to get, like, floppy loose, and I’m sure it was only a matter of time till it broke, and I didn’t want to see it break. Now it’s like my trophy because it’s my first so I can’t break it. So, we know now that if 30% infill in a printed AR lower with ABS will start to die around 2000 rounds, which is still ridiculous. I think it’s 70% hollow, which is hard to think about, but you get full control over, the internal fill whenever you’re 3D printing something. And, as a result, you could probably get like eight AR lowers out of one roll of fiberglass. I’m printing everything solid. So, I think six would be around the maximum. And again, it depends on how you set up your support, if you fail any prints or that sort of thing. And the lowers are quite strong.
Shane: Right, right. That’s not bad at all for $100 worth of material. That’s positive to hear. I think the last one we have to talk about is PETG, right?
Ivan: Yep. And so I threw PETG on this list just for my buddy, inCarbonite. He loves PETG; he prints lots and lots in PETG. PETG is sold as if it’s the strength of ABS, but it’s as easy-to-print as PLA. I agree with the “as strong as ABS.” It definitely is, but I have had more trouble printing PETG than printing ABS. I can’t get PETG prints to stop warping. I can’t get PETG prints to not be hideously ugly whenever I’m done printing them. That being said, I’ve maybe printed like one roll of PETG before I gave up, but I just have the darndest time printing with them. In general, I mean I can give you—well, I shouldn’t recommend temperatures or specs for PETG simply because I have terrible results with it. So, use whatever the manufacturer recommends. They know better than I do in this case.
But the advantage of PETG is it’s very chemically stable, so no chemicals will break it down. It’s got a glossy-like finish. There’s transparent PETG, and when I say “transparent,” don’t think it’s like looking through a glass window. You could maybe shine a light through it and you could see the lighton the other side, but it’s cloudy. It’s like cloudy glass is what it looks like.
Really that’s just about all I have to say about PETG. It’s an option and if you can get it to print right, you can get quite strong prints. Like, inCarbonite has all sorts of stuff he’s done in PETG, he’s done the glock frames in PETG, he’s done AR lowers in PETG, but I just have the darndest time working with it. And I know some other people are in my same boat, where we just can’t get it to run right. I think there’s people like inCarbonite who can do amazing things with it, but I feel like it’s worth mentioning just because some people find that it’s a less warp-y ABS.
And it sits price-wise around $20/kilogram as well. And you can print it easily on a Creality Ender.
Get the paperback book from Liberty Under Attack Publications!
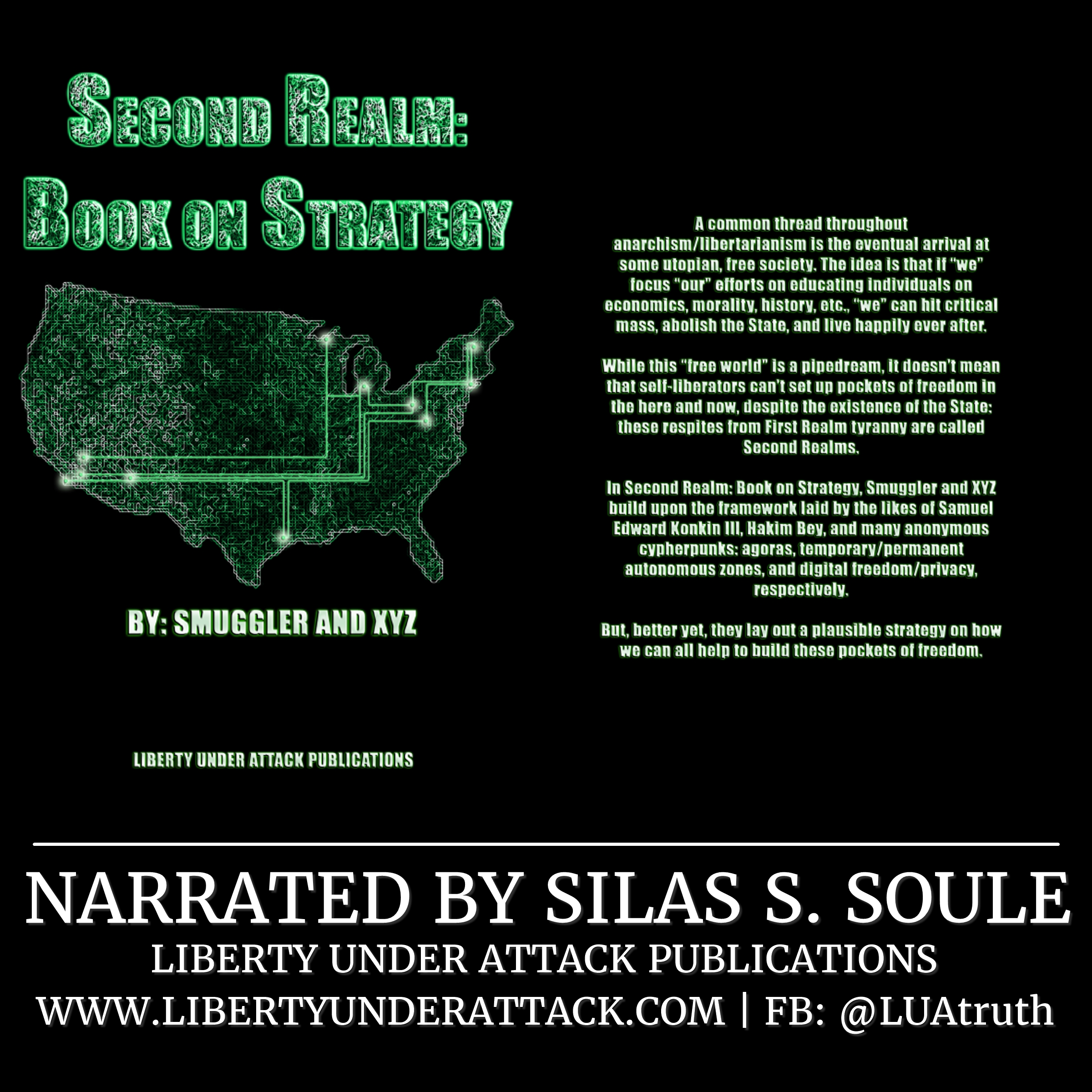
Get the audiobook for FREE! [Affiliate Link]
Shane: Very good. Yeah that’s positive to hear. So, I guess with a couple hundred dollar printer and maybe an upgrade on that printer and then you could have really nice nylon lowers then.
Ivan: Through all my testing on the fiberglass nylon lowers, and I’ve been putting a lot of time into that recently, I found that you cannot make one that’s invincible per se, which is kind of a bummer, because I really felt like I could for a while there. So, you can’t make one that’s like indestructible to the point where you have to really, really want to break it in order to break it. But you can make ones that are essentially like negligence-proof.
You might’ve seen it on my Twitter feed, I had been using fiberglass and fiberglass resin to reinforce lowers on the buffer tower. And even still with the reinforced buffer tower, it gave out after I maybe pushed myself up an inch. You can’t make one that’ll pass the pushup task, but you can make ones then that are, you know, they’re resistant to abuse, which is great.
Shane: Alright, very good. So, I guess the next to the next topic would be CAD and the software side of things now. When I downloaded the Liberator pistol a few years back, merely to look at it, as I didn’t have a 3D printer then, I still wanted to at least to open the files. So, I did a search and STL Viewer popped up. I downloaded STL viewer and was able to look at them and it didn’t print anything with it, but that’s the only software I’m familiar with in this realm. What software is out there? What’s the best and I guess most user friendly to use?
Ivan: Generally speaking, the best kind of CAD software that’s out there, at least for, say, beginners and the one that we’re trying to get people to standardize on is Fusion360. Fusion360 is made by AutoCAD and it’s partially cloud-based, which I know is a turn off for some people, because they don’t want any of their stuff in the cloud, but we did most of the AR 15 CAD assembly work on it; Jacob was doing all of it in Fusion. I did just a little bit of it in the app. Now, Fusion360 is very powerful, it’s free. You can get it free claiming you’re a student, and then you can download it with a student license. Essentially, you just check a box that says, “I’m not going to make more than $10,000 off of using this.”
And if you do make more than $10,000 a year off of using it, then Autodesk could sue you. And that’s what you’re agreeing to there. I’m a student and I’m not making money off of this, or you promise you’re not using it for your business. So, of course, you can get a free version that way. The free version for Fusion, I believe, offers you all of the tools, which is cool. So you can do everything in it and like it’s a full CAD studio for free, which is awesome. So, I do recommend Fusion just for that. It’s pretty darn easy to learn. There’s lots of tutorials out there for it, too, because it’s been free via the student method for quite a long time; lots and lots of people who’ve made tutorials. I won’t go too deep into, say, how it is you do things in fusion, simply because if you’re interested, download it.
Start on a tutorial that you can just Google or YouTube, like Fusion360 tutorial and you should be able to pick it up pretty quick. I think people tend to scare one another about CAD being hard. And I think a lot of that has to do with the, again, I’m going to make fun of boomers, but like boomers who learn to draw on 2D drawing boards hate CAD simply because it’s different. Meanwhile, I think like anyone, anyone who grew up in like the Internet or video game era is going to think CAD’s not that bad, because you’re used to using a computer, right? Grandpa grew up using pencils on a drawing board that was normal to him, and he wrote in cursive. That was normal to him. Just like we grew up on computers, that’s normal to us. So, CAD isn’t as bad as people make it out to be. That’s one kind of software that’s involved in the whole 3D-printed guns and stuff that’s known as a CAD studio or a CAD environment.
So, CAD software. The other kind of important software to know about is slicing software. What slicing software is, in a nutshell, is it takes your CAD model, and it converts it into instructions for your 3D printer because your 3D printer is really dumb. Like, I’ve described FDM machines as a computer controlling a hot glue gun. It really does think on a very, very stupid level. “Yes, I’m going to move the X axis this far, I’m gonna move the Y axis this far.”
It doesn’t know what it’s making. It’s just reading a list of instruction to, say, move this axis to this far, move this axis this far because your CAD model has to be converted to move this axis to this far, this axis to this far, and then that’s one layer. Then move this axis this far for the next layer. So, your slicer is what does that, your slicers or slicing software. There’s a couple of free slicing softwares out there. I believe Cura is free. I haven’t used Cura much at all, simply because Prusa has their own a slicer, known as Slic3er, that’s done specifically by Prusa. Although you can use their slicer for other printers, Prusa makes it in-house.
I think it’s got good features and it’s incredibly easy-to-use, but in general, the way your slicer works is you import your STL or your OBJ model file and then in your slicer, you choose what material you want to print it in, what settings you want, what kind of supports you want, how hot you want to print it, where exactly on the print bed do you want it, where you want to print it out on the print bed, what orientation you want the part in your slicers; you have full control over that. I think for people who are new to this, worry more about learning how to use your slicer than you do about worrying how to use CAD, simply because you can be great at using CAD, but you’re not going to be able to print much off if you don’t know how to use your slicer.
All sorts of tutorials out there for a slicer. It’s usually easier to learn than using CAD because the hard part about using the slicer is understanding what each term means. So, like number of walls, wall thickness, or what a raft is. All these things you’ll pick up on pretty quickly. Load up a roll of PLA on your printer, just draw a cube in CAD or download a cube STL file and just mess around in your slicer with all the different settings; load up a roll of PLA, do a whole roll of PLA, spend a day printing cubes. You’re looking at cubes and seeing how the different settings in your slicer affect what it is that you’re making. And once you’ve mastered that, I mean, by then, you’re essentially halfway to being great at this, because you’ve figured out your slicer. The other thing you have to figure out is CAD, and then you’re an unstoppable ghost gun maker at that point because you can throw your own CAD, print your own parts.
Shane: Right on. Real quick, Ivan, I think for the show notes to this episode—if you could, obviously we’ll do this afterwards, but for the types of printers, like one or two that you recommend, types of polymer, what’s you recommend, what you’ve had success with for CAD software, obviously Fusion, then whatever slicer you recommend, et cetera. It could be worthwhile to put that in the show notes. So we can just make it, people can just go to the show notes, click on Amazon, order a 3D printer, and go download the software they need you know from one spot.
So, I guess the last bullet point here in the CAD software section is file types; what do you mean there?
Ivan: With file types, it’s worth noting like when…I don’t know about you guys. Whenever I post like a video of me doing something, everybody shows up in the comments, specifically on Reddit, and they go like, “Can I get an STL? Can I get an STL? Can I get an STL?” And I make fun of them, because if you’re going to get into this stuff, please, for the love of God and Jesus and all the other powerful deities and everything that is Holy, do not just share STLs. I’ll explain why by explaining to you the difference in file types. So again, there’s like a triple hierarchy of file types. The best possible one is a native file. So, what a native file is, is inventor has it’s own file type, .IPT. Fusion360 has its own file type, I think it’s F3D.
SolidWorks has its own file type as SLDPRT. So, each one of these CAD studios has their own individual file type and that’s known as like a source file or in its source or native format. That’s probably the best file that you could share with people. What you can do with that is import any major CAD studios like NX, Simon’s NX, SolidWorks inventor, Fusion. They can all open one another’s native CAD files. And if you’re using the same studio as the person was using, so, if I’m in inventor and I send you a part and you open in inventor, you can see exactly the steps I made to make that part. And so you can edit the exact steps I made to make that part, which is very, very powerful tool. As folks out there who have learned CAD do begin to see it’s incredibly powerful to have the original source file for a part, incredibly powerful.
So, the next step down from the source file is known as a step file. I don’t want to confuse people with like names and definitions with the actual differences here between these files, but a step file, you can think of it as a native file, but it’s got no history of how that part was made. So, it doesn’t tell you that this part was made using this sort of operation and this sort of operation. It just takes that part, all of those operations, and converges them into one body and says this is the part. However, it is still a solid part. So, if I was to go and edit that part, if I wanted to make this hole a little bit bigger, I could create a new hole and then cut out a hole on top of where that hole was to increase the size of a hole. And so when that way step is editable, it just doesn’t have that history of how the part was made, which is an incredibly useful tool, but if you have a step file, you can always work with it. It’s not a hard way to do it, it’s just a little bit more tedious, but not terribly hard.
Now, we’re getting to the nitty gritty, the worst of the bunch, which is STL and also included miss batches, OBJ. I personally like OBJ better just because OBJ understands what units are, and STL files don’t understand what units are, which is a discussion for another time, it’s like gun printing 102, we can talk about this. STL files do not have a history of how they were made and they’re not a solid body. STL files are just like a mesh of faces; whenever you export a step file or a native file to an STL, your CAD software converts that into a bunch of flat faces because STLs also don’t understand what a circle is. Those of you who have taken calculus understand that you can approximate a circle by a multi-sided polygon. It’s like a 50 sided polygon, looks like a circle. And when it comes to printing that part, 50 sides on a polygon, it’s very difficult to tell that it’s not a circle at that point.
But that’s essentially what your STL file does; it converts anything that’s rounded to a flat face and it converts everything that’s already a flat face to a flat face. That’s what an STL file is. It’s just a bunch of faces merged together. Because of that, the 3D printer/slicer, and the slicer softwares can understand what STLs are because they’re a mesh of vertexes and faces. So, it can grab those texts and faces easily and translate them. Meanwhile, step is a solid body. It’s still defined as having actual circles and stuff. Those are the major differences between them and that’s the reason why if you’re sharing CAD files of any type, don’t be the guy that just shares an STL, because if eventually you disappear from the movement or your computer crashes or something bad happens, you’re going to lose all of that part history and all of that editability, and so you’re going to force someone to, one day later, manually go through and pull dimensions, one at a time, off of that STL part and convert it back into a native format, which I’ve done before. And it was really not fun. If at all possible, when you’re sharing CAD, share all three formats, because we know it takes you five minutes to convert it to each format. Just share it that way. That’s my PSA on file types.
Shane: Yeah, I can imagine that’d be frustrating to work with. So, you’re trying to have some sort of standard way of doing things. Very interesting. I guess here we get to some miscellaneous points on the outline and I’m curious about this, too. If I get a 3D printer, where do I buy gun parts, including non-printed upper and lower parts? Like, where do I get the stuff to start 3D printing?
Ivan: Specifically for finishing gun parts, like in the ReadMe for the Glock 17 frames, we had mentioned that Midway USA is a good site. Brownell’s is a good site. Specifically for Glock stuff, 80Pbuilder.com is a good site and generally fairly cheap prices. Brownell’s doesn’t have cheap prices right now, they’re pretty much always like 2% more expensive than anywhere for whatever reason. That being said, Brownell’s pretty much always has whatever it is you’re looking for in stock, where as other places don’t. I like giving business to Brownell’s, just because I like what Brownell’s does with like their retro rifles, but don’t support Brownell’s just because I support Brownells, unless you also think retro ARs are super cool. But, as far as if you want to build cheap AR-15s, I’m sure most people know about Palmetto State Armory.
If you don’t know about Palmetto State Armory, you need to learn about Palmetto State Armory. The first AR that I built on a printed lower, I finished for under $300. And you’re going to think, well, doesn’t that mean that it’s like crappy quality? I’m not going to name other companies because people get offended when you make fun of their crappy quality ARs. Palmetto doesn’t make crappy quality ARs. Some people think that they do. I think it’s just that Palmetto lets the lemons go out the door sometimes. I think overwhelmingly people getting ARs from Palmetto have exceptionally great experience with it. You know, the people who tell you it’s just as good as extra high quality, I don’t know that that’s the case, but I do know that Palmetto ARs are great. I’ve never had a misfire and I’ve never had a big problem with a Palmetto AR that wasn’t the fault of—so I’ve had misfires in Palmetto ARs, but they were built on a printed lower, and it was the printed lower’s fault.
Or I’ve had jams with using a printed magazine when it was a printed magazine’s fault. So, generally speaking, if you’re going for Glock parts, 80PBuilders is the way to go just because it’s so much cheaper than buying factory Glock parts. If you’re buying AR uppers, I think Palmetto State Army’s the way to go. Anderson is also sort of cheap. Midway USA, I think their in-house AR line is called AR Stoner and it’s also fairly cheap stuff. Cheap in terms of price, not cheap in terms of quality. I also have a couple Stoner ARs and they run quite well.
As far as buying ammo, AmmoSeek.com is the only thing that I use anymore. It just essentially compares all of the different sites out there and find you the cheapest in terms of cents per round. It’s essentially the only way I managed to afford all of the testing for the G17 because I had never had a 9mm gun before doing the printed G17. I ended up doing almost a thousand dollars’ worth of 9mm ammo. And the only reason I was able to afford that is because I had found it cheap on AmmoSeek. I had been paying the local sportsman store prices, which was expensive. It was like 25 cents a round and I was being scammed for it, whereas online, it’s like 18 cents or less, which is such a significant savings when your blowing hundreds and hundreds of rounds in a week of testing.
As far as parts for stuff that isn’t guns, you can get 3D printer parts all over the place. Amazon or eBay is generally your best bet. I buy practically all of my filament from Amazon. It sucks that you can only get the DuPont stuff from a company, a distributor named COEX. COEX charges far more for shipping than it costs them to ship, which is kind of a lame business practice. I think MatterHackers sometimes has the normal non-glass-filled, Zytel in stock and MatterHackers Printing is much more reasonable than COEX. I think that about covers like, you know, what it is that you would need to buy. You buy acetone from Walmart or whatever and tell them it’s for making meth and not for making guns, or else they’ll suspect that you’re making guns.
Shane: This came up a couple of times in the Twitter threads, when you announced this discussion. Common errors and troubleshooting: what are normal things that arise and what are some solutions to solving them?
Ivan: I would say the most common error is going to be your Z-offset. What that means is the height between your bed and your nozzle, the tip of your nozzle, always has to be set manually, at least on hobby printers. On industry printers, this is not the case, but on Prusas you have to set that distance manually, on Enders or Crealities, you have to set that distance manually. And until you get good at setting up distance manually, you’re not going to get good prints. You’re going to have prints that have horrible quality or they mess up badly in the middle of the print; all sorts of different issues you run into if your Z-offset isn’t right. In general, the way you want your Z-offset to work is just print a print that’s essentially just like a flat rectangle that’s one layer high.
You can draw this print in CAD or you can just set an extra wide brim or just print a nothing. Import a part that’s like nothing into your slicer, and then say that you want to print a raft point. So, watch as it prints that first layer; there shouldn’t be any gaps, so your first layer should go down nice and evenly. It shouldn’t look like your first layer is smushed so thin that you can see the bed through it. It shouldn’t look an extra-stretched out balloon where you can sort of see through an extra stretch out balloon. You don’t want it to look like that, but you also don’t want it to be so not smushed down, where it just looks like it’s a bunch of lines that aren’t touching each other. And so if you’ve got a printer you’ll be able to understand better what I’m saying here.
But if your nozzle is too far away from your bed, your plastic won’t be smushed down to form a layer. If you can imagine, take spaghetti noodles and make it into like loose rectangles where the noodles don’t touch each other. That would be a problem. Meanwhile, if you imagine you took that arrangement of noodles and smashed it with an anvil, if your nozzle is too close to your bed, it’ll do that. So, it squishes the noodle so far out that it’s not going to form a layer that way. The ideal is that it sort of creates like an oval-shaped blob as it goes and prints on the one line that it’s printing. It should sort of be about twice as wide as it is high, at least on your first layer.
As it’s printing, if it’s printing a rectangle, it should be a continuous rectangle. There shouldn’t be any air gaps and it shouldn’t be so thin that it looks like you’re looking through a stretched-out balloon. It should have some height to it, but it should also like each line that’s next to each other should, there shouldn’t be any air gaps. If it isn’t like that, then you probably have something wrong with your Z-offset. For podcast notes, I have some pictures that Prusa put out that should help you set your Z-offset.
Shane: Oh yeah, for sure. We’ll load up the show notes with lots of goodies. Just go to VonuPodcast.com/55 if you’re not listening on the podcast page. The next section here is just a section you titled “Food for Thought.” You want to cover those?
Ivan: So, whenever I was talking way earlier, I said we’d get to it later…well, now it’s later. What I want to talk about here is some more theoretical stuff. We have to like sit down and take out our tobacco pipes and wear our school golf caps or whatever, because we’re going to have a very gentlemanly conversation, or gentle womanly conversation. I propose that 3D printers in relation to making guns aren’t ever going to be THE answer, at least not until metal printing comes along. And even with metal printing’s here, I don’t think that you’re going to see 3D printing ever replace traditional means of manufacturing. I think that 3D printing is an answer to lots of the questions that are out there. Specifically, how do you make complex geometry?
Making an AR lower using traditional manufacturing methods is very difficult. I know, there’s the guy who casted an AR lower out of soda cans. Everyone loves to link me that video. Keep in mind, that guy also has incredible knowledge of machines. He’s a machinist without a doubt. He’s a machinist, even if the guy may claim to not be a machinist somewhere in the video. I don’t give a crap that dude’s a machinist, he’s smarter than a lot of the machinist I know. Dude is really, really sharp, making a lower out of casted soda cans. You can’t really easily make an AR lower on a mill. Not that easily. Meanwhile, you can be essentially an idiot and 3D print one; assuming you know how to run a 3D printer, you can 3D print your own lower.
You can’t be an idiot as far as a traditional manufacturing goes, I should say. What I’m trying to get at here is 3D printing is AN answer, but it’s not THE answer. It answers a lot of the questions.
Some of these questions are, how do you rifle a barrel? I think 3D printing offers you the answer there. And how do you make complex geometry? Guarantee to you, 3D printing is the answer there. How do you make ergonomic parts easily? 3D printing is the answer there. To touch on that rifling part, you can use 3D printing’s ability to print complex geometries as an ability to make advanced toolings.
So, you can make very specific tool shapes using 3D printing, and then use those tools to improve traditional means of manufacturing. Get that? You can improve traditional means of manufacturing using 3D printing. So, in the industry, this is known as like additive assisted technology. 3D printing is professionally known as additive manufacturing because it has to have a cool name. So, additive manufacturing assisted technology. I recommend everyone who’s listening to this to go check out The Veg Oil Guy on YouTube. He’s a British guy who does casting, but a lot of the metal casting he does, he uses a cheap 3D printer to make the investments for it. If you don’t know what an investment is, it’s essentially the part that you want to cast, which he 3D prints out of plastic.
Then, he uses that plastic part to make a mold. He melts the plastic out of the mold. Then, he pours aluminum or copper or brass or whatever into the mold. So, your end result is a metal casted part in the shape of what that printed part used to be, and in the industry, that’s known as the additive assisted casting, AAC, which has be like a really big up-and-coming thing. I believe BMW is making entire engine blocks this way now, where they’re using a 3D printer that prints in sand. So, they print this in like bonded sand and then they use water to wash the sand out after they cast this stand in a mold, and then they washed the bonded stand out, leaving you with an investment of an engine block.
So then you pour your metal in there, and now you’ve cast an engine block, and your tooling was nothing. Your tooling was sand. Sand costs nothing; running a 3D printer costs next to nothing. Those are huge advancements being made in the industry there, as well as, I believe by now people have lost metal cast-AR lowers, that if you wanted aluminum AR lowers, not to knock on the guy that made the soda can lowers, but here’s the way to do it.
Bust out your Ender, open the CAD assembly we have for the accurate AR lower, print that AR lower, even though it wouldn’t work as a printed lower. Lost PLA cast it using Veg Oil Guy’s technique and his set up, and now you’ve got an aluminum AR lower and your tooling was what, a 3D printer in a sheet metal forge? So, it becomes abusable in that way. That’s one way that 3D printing technology’s abusable, is additive assisted casting. Another way that it’s abusable is what me and [Name] has sorta demonstrated on the rifling of barrels. You can do what’s known as, I guess, additive assisted electro-chemical machining. We need to come up with a better acronym, but using this additive assisted electro-chemical machining, you can use the fact that 3D printers can make a complex geometry, such as rifling groups, and you can use that to then rifle barrels very easily using electro-chemical machining. Because, traditionally, electro-chemical machining, the one caveat to it, is your tooling has to be as at least as complex as the part you want to make, because it can only—the shape that your tool makes is the shape that it’s going to cut. So, your tool ends up having to be as complex, or more complex, than the part itself you’re trying to make. But using a 3D printer, it’s not hard to make complex shapes, especially whenever there’s no heat and there’s no wear forces involved in an electro-chemical machining. There’s no heat, there’s no wear forces. So it becomes like a perfect compliment. One big question that had always been in there surrounding electro-chemical machining, well, there’s your answer in the form of additive assisted technology.
That’s sort of where I leave my scripted part of this, is I don’t think of 3D printing as we’re going to 3D print entire guns. Think of 3D printing as it’s going to make making a gun incredibly easy without having to print it.
Shane: Very good and well said. I think Cody’s [Wilson] response and my interview with him was similar, kind of the additive assist technology portion of it. Now onto some listener questions… A really good question here and I guess you might’ve alluded to it a little bit here. What can we do with a $400 printer that can’t be done on a $200 printer?
Ivan: So, to reiterate, I think this is just my way of thinking. Anyone else out there is free to think differently, because there’s not…some things I think I put my foot down on, mostly because I think I have an informed opinion, but I’m not putting my foot down on this because you all are free to spend your money any way you want. But I would only ever buy something that’s full feature like a Prusa or that’s bare minimum like an Ender. There are more expensive Creality printers, there’s an Ender Five, and I think the Ender Five is right around $400. I forget what exactly the Ender Five offers, but it’s not worth $200 to me. It might be automatic bed leveling, but I wouldn’t take $200 for automatic bed leveling alone.
It’s something where, as soon as you learn how to bed level, it’s not even a problem anymore. Especially because as long as you don’t move your printer around ever, if it just sits on the same table, you won’t ever have to re-level your bed, maybe save for like once every several hundred hours of printing.
So, what’s the difference? I mean, without knowing a specific $400 printer and a specific $200 printer, I can’t really tell you the difference. But, in general, you’re going to get more of those features, like a glass surface for your printer bed. Eventually, you’ll get into the price range where it’s not a direct Teflon-on heater block potted. Eventually, you’ll get up into like full metal hot ends where there isn’t a Teflon tube in it at all, all. You’ll run into printers where it’s got automatic bed leveling and where it’s got quick detach beds, those sorts of things, or more print augmenting as you’ve increased in price.
Shane: More features basically, that makes sense. Then again, $400, like to get to get a couple of those other nice features, that’s still not a bad price for a 3D printer. Still, maybe a little much for someone who may just be concerned considering it as a hobby. But $400 is not bad at all. You might’ve also alluded to or answered this question, but when and why do you print with PETG instead of PLA plus?
Ivan: I never print with PETG, and the reason why is because I can’t print with PETG to save myself. But if we’re to incorporate this question of like, “when do you not print with PLA?” Anytime where your use case is going to be getting very hot. PLA’s biggest drawback unfortunately is it can’t handle hot operating environments. So, for example, if you left PLA in a hot car and direct sunlight, it would start to melt and deform completely. If you left PLA in a hot car, it would become soft. So, if there’s any force outside acting on it, it will deform. But in direct sunlight, it’ll melt into like a puddle. So, any use case requiring there to be fatigue forces on it.
Don’t use PLA for the reasons that I overelaborated on before. PLA isn’t really good at reciprocal loading, so it doesn’t like to load and unload, and load and unload. That’s a sin, eventually how you break PLA parts because of its crystalline structure. So, anytime where you need flexibility, anytime where you need it to be able to stand up to the heat, don’t use PLA. That said, people tend to misunderstand when it is that you need heat resistance and when it is that you don’t. The glock frames that I’ve printed have been in PLA. I printed a couple in the high-strength glass-filled nylon, but most of the ones, like the one I use, are in PLA. You can dump a mag and then reload, and dump a mag and reload, and it still won’t be hot enough to even make the PLA start to become soft.
So, under normal use of a firearm, PLA isn’t going to be getting too hot. If you’re in a hot environment, say 110 degrees in the desert and you start dumping mags, you’re probably going to get to that threshold, especially if you take a drum mag and dump it. I guarantee you you’ll get it hot enough that their frame will start to warp in your hands. But under normal operating conditions, I wouldn’t imagine it would be a problem. To conclude, no hot environments and no loading and unloading like on an AR buffer tower.
~~~
~~~
Shane: All right, fair enough. So, someone else asked the question on Twitter. Basically, it’s great hearing how-to’s and what TO DO, but what about what not to do when printing 3D parts for guns?
Ivan: Let’s see, what not to do? Don’t tell the ATF about the auto sears. Don’t tell the ATF about the short-barreled rifles. Don’t tell the ATF about the suppressor baffles. Other than that, I’m joking. I haven’t printed any of those things referenced, nor do I have any intent to Mr. ATF Agent, I’m sure is listening to this. And Mr. NSA Agent that I’m sure is recording this conversation as it’s going on live. But, as far as what not to do, apparently don’t sniff the ABS fumes. It’s probably too late for me, but you guys don’t do that.
What not to do… So I’m going to use the double negative here. What not to do is not read the ReadMe; always read the ReadMe, the ReadMe in all caps. It’s a text file that can open in any native format, you can even read it in your web browser. The reason that I spend hours and hours typing up a read me, and then Deuces from FOSSCAD spends hours and hours formatting it, spell checking and error-checking my ReadMe’s, is because we intend for you to read them. A lot of people don’t like to pick up on it.
At first, I was like, “Yeah, okay, some people don’t do it,” but I swear, I get at least an email a day for the past several months. Like people asking me, “So, what should I print the Glock frame in?” Are you stupid? It says in this great big ReadMe that we have like a professional letterhead and everything on, it says it’s print it in PLA or Zytel or whatever the hell else. I don’t care, just print it. I don’t care. But the stupid questions that the ReadMe answers and these people don’t bother to read the ReadMe.
At first, I did explain it to people nicely, but eventually it just became like README in all caps as the response they get. But I have not yet not responded to anyone because I do like to respond to people. It’s just that I’m going to be snippy when I do it because if you can’t read, then I’m not going to be very polite. Sorry. People, learn to read, I guess.
Shane: Any other what not to-do’s? Like, is there something that one might be inclined to do that would be a dangerous thing to do? Are there any kind of obvious things that you wouldn’t think you’d have to tell somebody? Those are still worth mentioning.
Ivan: Don’t bypass any software safeties on your machine. They are there for a reason. If you upgrade your hot end, of course, that’s an exception, because then you can increase the max temperature to 300° Celsius, but otherwise, the restrictions in your machine are there for a reason. And that reason is so you don’t burn your house down, unless you’re looking to scam your insurance company, in which case, take those restrictions off, but don’t tell anyone you did it. Like when it comes to assembling guns, this one’s going to come in three parts… when it comes to assembling guns, when it comes to letting spray paint dry, and when it comes to letting fiberglass resin set up, don’t rush it.
I say this full well knowing that I never obey this rule; the whole time the spray paint’s drying, I try to touch it, so I leave fingerprints in it. The whole time fiberglass resin is setting up, I touch it. So, I leave fingerprints in it. Like, the whole time I’m assembling guns, I always just want to rush through it and try and find the quickest way to do it. So, I’ll just go nuts with a dremel tool and sand more, take more off than I should have. Because instead of going slow and measuring, you know, cut a little bit, measure a little bit, I want to cut a lot and then measure it and go, “Shit,” afterwards. So, in general, go slow.
I say this knowing that I will never obey such a rule, but go slow and take your time.
And, it’s not dry yet.
[/end Gun Printing 101 with IvanTheTroll]
One Reply to “Gun Printing 101 with IvanTheTroll (Podcast/Transcript!)”